What is Wiring Harness?
Table of Contents
What is Wiring Harness?Definition of wiring harness
Wire harness, also known as cable harness or cable assembly, is an integrated unit formed by carefully combining and bundling multiple wires or cables. It is like the “nervous system” in modern transportation and various complex equipment. In the automotive field, it connects all electrical and electronic (E/E) components such as sensors, electronic control units, batteries, actuators, etc., to ensure that the vehicle’s main functions such as steering and braking, as well as secondary functions such as ventilation and infotainment can be smoothly realized.
If all the wires in the car are unfolded, the length can reach several kilometers, and the wiring harness can bind them in order, effectively resisting the adverse effects of vibration, wear and moisture. It not only optimizes space utilization and reduces the risk of short circuits, but also greatly shortens the installation time and is easy to standardize because only a single wiring harness needs to be installed instead of multiple wires. At the same time, the use of flame-retardant sheaths reduces the risk of electrical fires.
In the aerospace field, from drones, satellites to airplanes, wiring harnesses ensure key links such as power transmission and communication; in the medical industry, ambulances, diagnostic and imaging equipment, dental equipment, etc. in hospitals and clinics rely on wiring harnesses to organize and protect internal lines; in the telecommunications field, modems, routers, repeaters and other equipment use wiring harnesses to optimize space utilization; in the field of information technology, computers, notebooks, servers, etc. are also inseparable from wiring harnesses to organize wiring, which is convenient for technicians to identify and install; in the construction field, wiring harnesses provide insulation and orderliness for wiring in buildings; in the manufacturing industry, equipment such as CNC machine tools rely on wiring harnesses to plan internal and external lines; in the robotics and automation industry, automation equipment and robots rely on wiring harnesses to safely route, group and protect key lines.

Manufacturing process of wiring harness
Design stage: With the increasing electronic content of automobiles and other products, wiring harness design has become more complex and time-consuming. First, the electrical system engineer defines the functions of the entire electrical system, including electrical loads and special needs, and considers the status of electrical equipment, installation location, and the connection form between the wiring harness and the equipment. Based on these, a complete vehicle electrical schematic is created, and the components required for the function are added and connected.
The common functions of multiple vehicles on the same architecture platform will be stored centrally. Then the wiring harness design is carried out. Considering the diverse needs of end customers on the same platform, designers need to take into account multiple variants to avoid the high cost and long cycle caused by separate designs for each customer. Finally, a 2D wiring harness diagram is generated to show the wire bundling and covering methods and the end connectors. This design can interact with 3D tools to import and export data such as wire length and connection details. The 3D tool adds passive component information such as cable ties, cable ties, cable braids, sleeves, electrical tapes, and conduits and then returns it to the wiring harness design tool.
Production stage: After the software design is completed, the wiring harness is produced in the manufacturing plant, passing through the cutting area, pre-assembly area, and finally assembled in the assembly area.
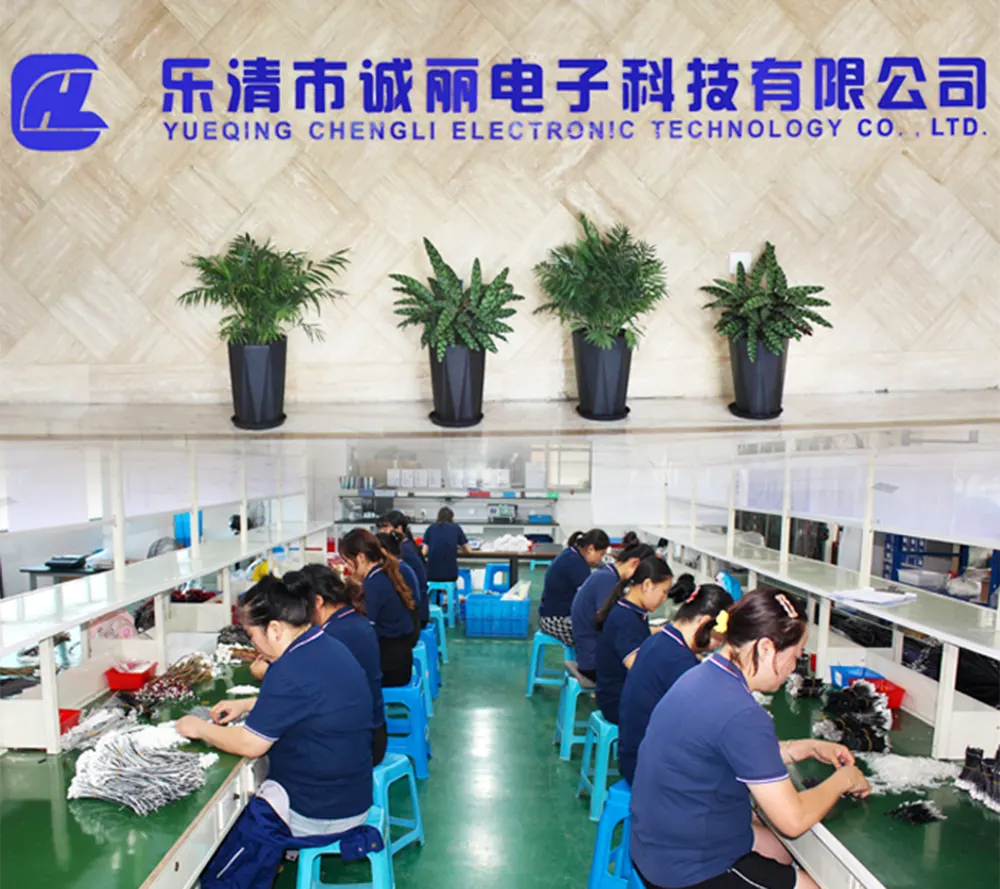
Challenges faced by wiring harness manufacturing
Inconsistent data and limited reuse: Global teams use different EDA and CAD tools to design, which can easily lead to inconsistencies in “shared” data over time, making it difficult to reuse designs, affecting product time to market (TTM), and consistency issues discovered later often need to be resolved in the early design stage.
Insufficient system integration: Inconsistencies and design quality issues are discovered when the designs of global decentralized teams are merged, which is close to the end of the project, affecting TTM and consuming engineering resources. When vehicle requirements in the project change due to competition or new standards, platform updates require changes to all tools and databases, which are prone to errors and omissions. The lack of continuous system integration will increase the risk of data inconsistency and merging difficulties.
Late exposure of problems in the physical prototype stage: Even if the design merger goes smoothly, problems may still occur in the physical prototype construction and testing stages of the electrical system. Repairs will further delay TTM and consume more resources. Traditional process design analysis is limited and relies on laboratory test verification. Using better EDA tools can be more fully verified before physical prototypes, and only the laboratory can do final system verification.

Advantages of using EDA tools to manufacture wiring harnesses
Better data consistency: Tools and methods support platform-driven design generation, and ensure data consistency and full reuse by connecting the design process from top to bottom and integrating with “correct construction”, which affects TTM.
Data integrity: All functions are designed collaboratively, with a single design database, option processing and multi-user concurrent design environment to avoid design quality problems caused by lack of integration.
Design verification: Integrated simulation at all levels, using built-in simulators for advanced verification and automated rapid setup and reuse, ensures that problems and errors are found in the design stage, improves circuit robustness and quality, and can also explore the design space and analyze more design permutations and combinations, which is more efficient than building and testing multiple physical prototypes.
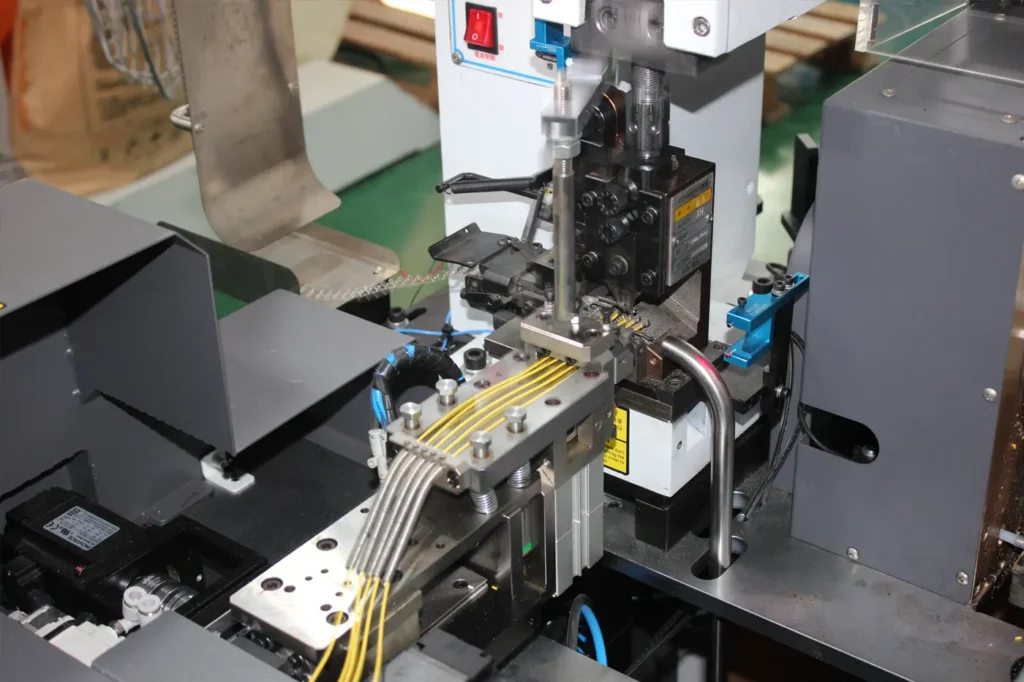
Key points of custom harnesses
Component selection: Custom harnesses can be assembled on demand, including wire ties, braids, various insulation materials, custom colors, heat shrink coatings, custom labels or barcodes, four-color ink stamping, individual markings, independent circuit IDs, fillers such as polypropylene, custom shielding and other components. Suitable insulation materials can also be selected according to needs, such as PVC, SR-PVC, honeycomb polyethylene, EPDM, TPE/TPR, PE and other options. When selecting materials, environmental variables should be considered, such as waterproof polyethylene for humid environments.
Considerations: When evaluating new harness solutions, consider the use environment, temperature conditions, applicable voltage (up to 600 volts for civilian use and 3000 volts for military use), whether it is continuously bent, indoor and outdoor use scenarios, circuit and conductor quantity characteristics, potential chemical and other exposure risks, operating temperature fluctuations, local safety and environmental regulations, and wiring, branching, appearance, etc.
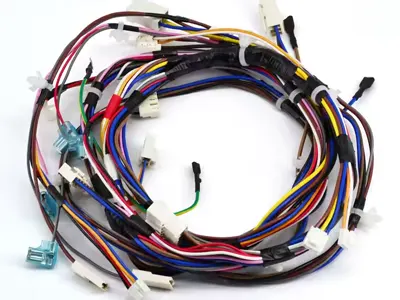
Wire harnesses play a key role in many industries with their simple and efficient design, reducing costs, optimizing organization, shortening installation and maintenance time, and improving safety for various systems. They are indispensable basic components in the field of modern engineering. Whether it is large-scale industrial production or customized high-end applications, it is inseparable from the in-depth understanding and precise application of wiring harnesses.
One Comment