Tesla’s Wiring Harness Requirements
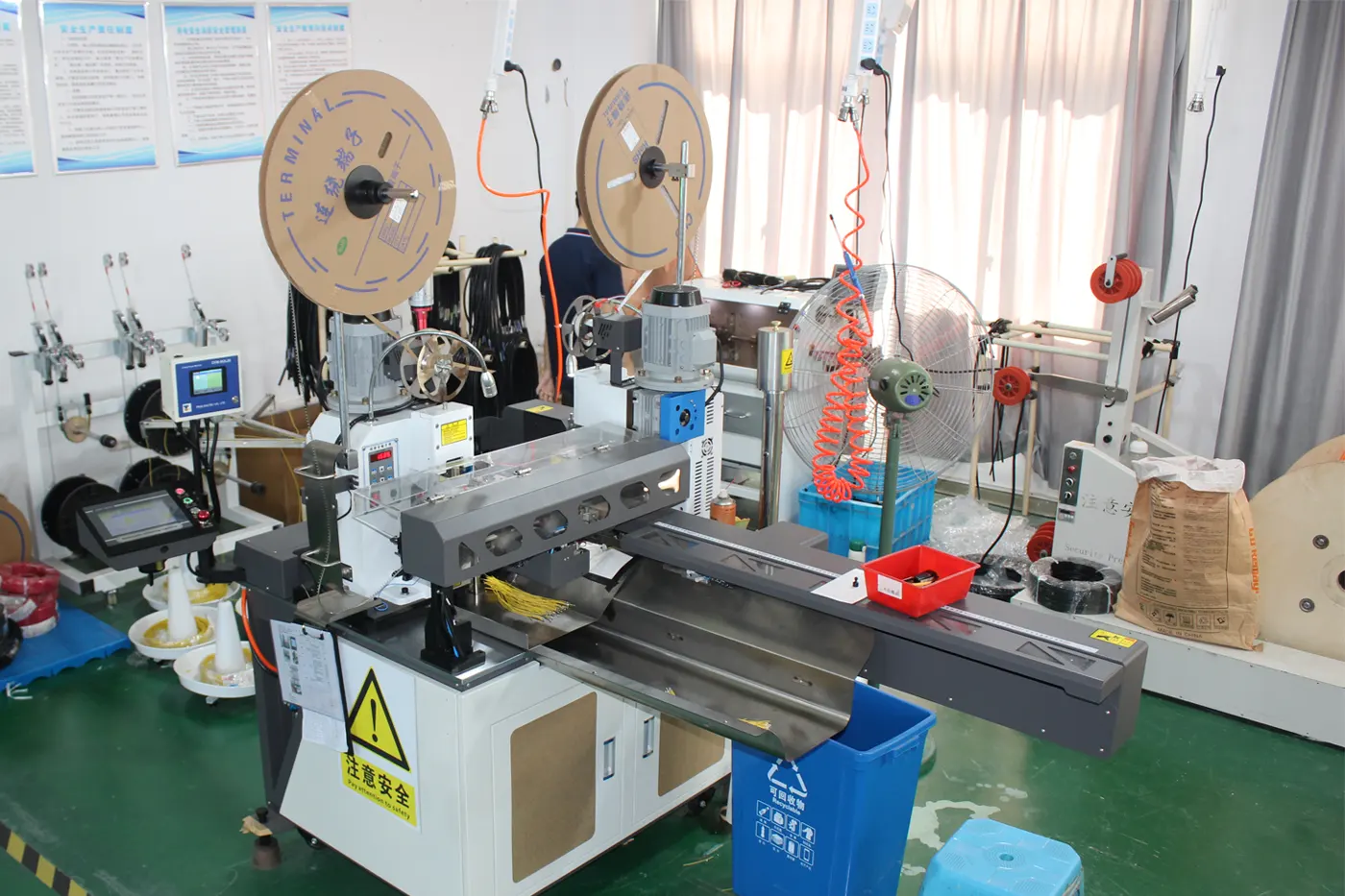
Tesla places strong emphasis on advanced wiring harness requirements to ensure safety, efficiency, and innovation in every car. High-quality wiring harnesses play a vital role in electric vehicles like the Tesla Model S. These harnesses:
Support critical safety features and automation by connecting sensors throughout the vehicle.
Enable efficient battery charging and power delivery, which improves range and performance.
Allow integration of high-tech features for added comfort and convenience.
Leading manufacturers such as Yueqing Chengli meet these strict wiring harness requirements for modern vehicles by providing reliable solutions that withstand tough conditions.
Key Takeaways
Tesla designs wiring harnesses to be shorter, lighter, and more reliable, which improves vehicle safety and efficiency.
Strict safety standards and certified technicians protect both workers and the vehicle’s high-voltage systems.
Suppliers like Yueqing Chengli meet Tesla’s high-quality and environmental durability requirements through advanced materials and certifications.
Tesla’s simplified wiring architecture reduces complexity, lowers weight, and supports advanced features like fast data transfer and autonomous driving.
The move to a 48-volt system boosts energy efficiency, extends driving range, and prepares Tesla vehicles for future innovations.
Wiring Harness Requirements
Technical Specs
Tesla sets the bar high for wiring harness requirements in electric vehicles. The company’s technical approach stands out in the industry. Tesla engineers design harnesses to minimize length and complexity. For example, the Model S used about 3 kilometers of wiring, but the Model Y reduced this to nearly 100 미터. This drastic reduction results from tight integration of components and advanced system architecture. Tesla also uses robots for assembly, which increases precision and consistency. Most traditional manufacturers still rely on manual labor and longer, piecemeal harnesses. Tesla’s focus on automation and integration leads to fewer connection points and less risk of failure.
Yueqing Chengli meets these wiring harness requirements by offering customizable solutions for electric vehicles. Their products support high-voltage wiring harness needs, ensuring efficient power delivery and communication between vehicle systems. The company’s advanced manufacturing processes allow for rapid adaptation to Tesla’s evolving technical demands.
Safety Standards
Safety remains a top priority for Tesla’s wiring harness requirements. The company enforces strict technician qualifications and repair protocols. Only certified technicians may work on high-voltage wiring harness systems. They must wear personal protective equipment, such as class 0 gloves rated for 1000V. Before any repair, technicians verify the absence of voltage using specialized meters. Jewelry and metal objects must be removed to prevent accidental conduction. Test equipment must meet a minimum rating of 500V DC. Tesla requires a specific order for voltage measurements and assumes high voltage is present until proven otherwise. If equipment malfunctions, technicians follow lock out–tag out procedures. Electrical safety hooks remain available for emergencies. All repair instructions must be fully understood before starting work.
Note: These protocols protect both technicians and the high-voltage system, reducing the risk of injury and ensuring the integrity of the vehicle.
Yueqing Chengli’s wiring harnesses comply with global safety standards. The company holds certifications that guarantee product safety and reliability.
인증 | Focus Area | Contribution to Supplier Reliability for Tesla |
---|---|---|
ISO 9001 | Quality Management | Ensures consistent product quality and customer satisfaction, indicating reliable quality control processes. |
IATF 16949 | Automotive Quality | Specifically required by automotive manufacturers to reduce defects, prevent mistakes, and save costs, directly supporting Tesla’s high standards. |
ul | Product Safety | Certifies product safety compliance in the U.S., ensuring wiring harnesses meet strict safety requirements. |
CE | European Compliance | Confirms compliance with European safety and regulatory standards, enabling suppliers to meet global market demands. |
These certifications show that Yueqing Chengli can meet Tesla’s wiring harness requirements for safety and quality.
Environmental Durability
Tesla’s vehicles operate in a wide range of environments. The wiring harness requirements demand durability against temperature changes, 수분, and vibration. High-voltage wiring harness assemblies must withstand harsh conditions without losing performance. Tesla tests harnesses for resistance to heat, cold, and corrosion. The high-voltage system must remain stable even in extreme climates.
Yueqing Chengli designs wiring harnesses with robust insulation and corrosion-resistant connectors. Their products use materials that comply with European environmental protection standards. This commitment ensures that each high-voltage wiring harness performs reliably over the vehicle’s lifetime. The company’s experience with global clients demonstrates their ability to deliver durable solutions for demanding applications.
Design and Integration

Simplified Architecture
Tesla’s approach to simplified architecture sets a new standard in automotive wiring architectures. The company uses an Ethernet ring network in models like the Cybertruck. This new wiring system replaces traditional bundles with lightweight, high-speed communication lines. Thinner wires and less copper lower both weight and cost. The design reduces manufacturing complexity and the number of possible failure points. Tesla’s focus on minimizing complexity and weight leads to greater efficiency and reliability in every car.
Tesla’s simplified wiring harness architecture allows for more robotic automation during production. This change speeds up assembly and reduces errors.
Wiring Harness Design
Tesla integrates wiring harness design with the overall vehicle platform. The company uses flat, modular harnesses instead of flexible round conductors. Local controllers in subassemblies, such as doors, manage devices nearby. This modular approach shortens cable length and reduces complexity. Subassemblies can be pre-assembled and tested before joining the main platform. The Cybertruck’s ethernet-based system connects high-speed controllers, cutting wiring mass by 84%. The backbone structure with specialized cables and connectors improves both power and signal transmission. Tesla’s design reduces the number of wires from 490 in the Model 3 to only 155 in the Cybertruck, even as the number of endpoints increases.
Advanced Features
Advanced features in Tesla’s wiring harness give the company a competitive edge. Many competitors use older connectors and heavier wires, which add weight and increase failure points. Tesla’s clean-sheet design avoids these legacy issues. The market for electric vehicle harnesses is growing as cars need higher voltage systems and more data transmission for autonomous driving. Tesla’s lightweight, modular harnesses support these demands. The streamlined design also prepares Tesla for future 48-volt systems, which will use thinner wires and improve energy efficiency. The new wiring system allows Tesla to adapt quickly, while competitors face more challenges with their older designs.
High-Voltage Wiring Harness

Power Delivery
Tesla’s high-voltage wiring harness plays a crucial role in delivering power efficiently throughout the vehicle. The company uses advanced cables, such as the 150 XLE High Voltage Shielded Battery Cable, which offers flexibility and reliability even in tight spaces. Tesla protects these cables with self-coiling braided sleeves inside the cabin and corrugated conduits in harsher environments, like near the rear drive motor. This approach ensures the high-voltage wiring harness system remains durable and dependable.
Tesla’s transition to a 48V architecture in vehicles like the Cybertruck marks a significant step forward. By increasing voltage, Tesla reduces current, which leads to much lower power loss. This change allows for smaller wires, lighter harnesses, and simpler electronic components. The result is a more efficient high-voltage system that supports the power battery system and modern vehicle features.
Shielding and Safety
Safety and reliability stand at the center of Tesla’s high-voltage wiring harness requirements. The company enforces strict handling procedures to prevent contamination from grease, oil, or water, which could cause electrical tracking or high resistance. Only certified technicians with High Voltage Awareness certification may work on the high-voltage wiring harness system. They must wear insulating gloves rated for at least 1000V and follow specific disablement procedures before starting any work.
Note: Tesla’s safety protocols include removing jewelry, using only approved greases, and ensuring connectors are secure and free from contaminants. The high-voltage system features automatic disconnects that activate if hazardous conditions arise, protecting both the vehicle and the technician.
Tesla’s detailed service manuals guide every step, from removal to storage, ensuring the high-voltage wiring harness remains safe and reliable throughout its life.
Gigabit Ethernet & CAN Bus
Tesla’s high-voltage wiring harness also supports advanced communication systems. In the Cybertruck, Tesla replaces the traditional CAN bus with a gigabit Ethernet architecture. CAN bus, while reliable for basic control, cannot handle the large data streams needed for autonomous driving. Gigabit Ethernet delivers high bandwidth and low latency, enabling real-time communication between local controllers.
Gigabit Ethernet allows for rapid data transfer, supporting features like steer-by-wire.
Power over Ethernet lets the same cables deliver both data and power, reducing wiring complexity.
Tesla’s modular system connects distributed controllers, making the network more flexible and efficient.
The integration of gigabit Ethernet and CAN bus improves data transmission, reduces wiring complexity by up to 77%, and supports the flexible, software-defined networks required for modern electric vehicles.
Quality and Supplier Expectations
Quality Control
Tesla and its suppliers use strict quality control processes to ensure wiring harness reliability. They follow industry standards such as ISO 9001, IPC-620, and UL approvals. These standards help keep every wiring harness safe and consistent. Custom quality testing is built into the manufacturing software. This step helps achieve zero defects in shipped products. Teams use kitting, sorting, and rework services to reduce defects during production. Expert sorting and on-site support keep quality high throughout assembly. Each assembly is designed and built for specific electric vehicle projects. This focus ensures durability and reliability. Supply chain management practices help maintain timely delivery and prevent production delays. These steps support continuous production lines and reduce downtime.
Traceability
Traceability plays a key role in wiring harness production. Every component receives a unique code. This code tracks the part from raw material to finished product. If a problem occurs, teams can quickly find and fix the issue. Documentation records every step of the process. This record helps Tesla and its suppliers meet safety and quality standards. Traceability also supports fast recalls if needed. Yueqing Chengli uses advanced tracking systems to ensure each wiring harness meets strict requirements.
Supplier Capabilities
A qualified supplier must show experience, flexibility, and a strong global client base. Yueqing Chengli stands out with over a decade of industry experience. The company serves clients worldwide, including major brands in automotive and appliances. Eco-friendly practices guide their production, using materials that meet European environmental standards. Fast turnaround and scalable production help meet Tesla’s changing needs. Reliable documentation and export support make Yueqing Chengli a trusted partner for complex projects.
Impact on Performance
Efficiency
Tesla’s wiring harness requirements drive significant gains in efficiency. The company’s move to a standardized 48-volt electrical connector in the Cybertruck architecture allows the car to operate with only 25% of the current needed by traditional 12-volt systems. This reduction in current lowers energy losses and supports a lighter car design. Lighter wiring harnesses mean less weight for the vehicle to carry, which directly improves energy consumption and extends driving range. The new connectors also simplify manufacturing and reduce costs. Robust sealing and independent locking mechanisms cover over 90% of electrical applications, streamlining the car’s electrical system and making it more efficient.
Reliability
Reliability stands as a core benefit of Tesla’s advanced wiring harnesses. The company uses high-quality materials and precise manufacturing processes to ensure each harness performs under tough conditions. Strong insulation and corrosion-resistant connectors protect the wiring from heat, 수분, and vibration. These features help the car maintain stable performance over time. Each component receives a unique code for traceability, so teams can quickly address any issues. This focus on quality and traceability reduces the risk of electrical failures and supports long-term reliability for all vehicles.
Future Innovation
Tesla’s wiring harness innovations shape the future of electric vehicle technology in several ways:
그만큼 48-volt architecture increases efficiency and driving range by reducing current and energy losses.
Auxiliary systems like HVAC, infotainment, and active suspension perform better, improving comfort and handling.
Thinner wiring harnesses lower overall vehicle weight, boosting efficiency.
The 48V system creates a stable platform for advanced driver assistance and autonomous features.
Regenerative braking and thermal management systems operate more efficiently, enhancing safety and battery life.
The scalable electrical platform supports the growing demands of modern electric vehicles.
Tesla’s approach to wiring harness design not only meets today’s needs but also prepares each car for future advancements in technology and performance.
Tesla’s wiring harness requirements set a high standard for safety, 성능, and innovation in electric vehicles like the tesla model s. Choosing certified and experienced suppliers brings long-term benefits:
They ensure regulatory compliance and reduce risks.
They foster innovation with advanced features and sustainable practices.
They manage supply chain risks and support production efficiency.
These practices help Tesla lead the industry and shape the future of electric vehicle technology.
FAQ
What makes Tesla’s wiring harness different from traditional car wiring?
Tesla uses shorter, lighter, and more integrated wiring harnesses. This design reduces weight, increases efficiency, and supports advanced features like autonomous driving.
Why are certifications like ISO 9001 and IATF 16949 important for suppliers?
Certifications show that a supplier meets strict quality and safety standards. They help ensure that wiring harnesses are reliable and safe for electric vehicles.
How does Yueqing Chengli support Tesla’s wiring harness needs?
Yueqing Chengli provides custom wiring harnesses that meet global standards. The company uses advanced materials and manufacturing processes to deliver durable and efficient solutions.
What is the role of traceability in wiring harness production?
Traceability allows teams to track each part from start to finish. This process helps quickly find and fix problems, ensuring safety and quality.
How do Tesla’s wiring harnesses improve vehicle performance?
Tesla’s wiring harnesses lower vehicle weight and energy loss. They support faster data transfer and make it easier to add new features in the future.